スパッタリングとは、真空中でプラズマを用い成膜する工法です。様々な材料に加飾ができ、密着性に優れ、制御がしやすいです。こちらの記事では、そのスパッタリングの特徴と実際の製品事例をご紹介いたします。
スパッタリングの原理
スパッタリングは、物質にイオン等を高速で衝突させることにより、分子が叩き出される現象(スパッタリング現象)を利用して、対象物にコーティングや表面改質を行う技術です。
真空条件下で、アルゴンや窒素など反応性の低い原子、分子を一定圧力で装置内に流し、薄膜の材料となるターゲットに高い陰電圧をかけて装置内のアルゴンや窒素をイオン化して照射すると、原子がターゲットから飛び出してきます。その飛び出してきた原子を、陽電圧をかけた対象物の表面に堆積させて薄膜を作製します。
真空状態で処理を行うため、不純物の少ない薄膜形成ができ、イオンの電気的性質を利用しているので、膜の強度を高くすることが可能です。
また、アルゴンや窒素の代わりに酸素を流し、酸化物の成膜を行う事もできます。
スパッタリングの特徴
スパッタリングの特徴として主に下記5つが挙げられます。
①付着力が強い
電気エネルギーをかけて入射するため、付着強度が増します。
②ステップカバレッジ(段差被覆性)に優れている
プロセス圧力が高いため、平均自由工程が短く、飛行途中の成膜原子の異方性を強めるため、散乱が起きます。
③膜厚分布が比較的取りやすい
ターゲットが広く、成膜プロセスが安定しているので、膜質・膜厚の制御も高精度で行うことが可能です。
④合金・高融点金属膜の組成制御がし易い
高融点金属・合金・化合物の成膜に適しています。
⑤カソード(電子が流れ込む電極)などの設置方向に制約がない
スパッタリングの種類
①2極スパッタリング法
2極スパッタリング法は、スパッタリング成膜技術の基本です。
ターゲットを陰極、薄膜形成する基材・基板を陽極として電圧を加え、ガスイオン原子でターゲット表面を叩き、飛び出したターゲット材料物質の粒子(原子・分子)が基材・基板に堆積する方法です。
2極法の装置構造は簡単ですが、不活性ガスをイオン化するグロー放電を起こすためのガス導入量が多く必要となり、その導入ガスが障害となって成膜速度が遅くなるというデメリットがあります。また、イオン化した負イオンなどの二次電子が陽極に照射されて、基材・基板が高温となってしまうという問題もあります。
②マグネトロンスパッタリング法
ターゲット側に磁石を設置し磁界をつくり、プラズマを試料から分離する方法です。電圧をかけてスパッタを行います。磁界により、電子が磁力線にそり、螺旋状に運動するため、集中的にスパッタすることが可能です。
③イオンビームスパッタリング法
イオンをターゲットや試料と別の場所でつくり、ターゲットに加速してあてる方法です。イオン銃(イオン発生器で発生させたイオンを加速して放出する装置)から放出されたイオンは、ターゲットに照射されスパッタします。
イオン銃には持続的にイオンを発生させるため不活性ガスが供給されます。
※原料自体をイオン化して直接試料にぶつけるのはイオンプレーティングと呼ばれています。不純物が混ざらないメリットがあるが装置が複雑になるため、高価になります。
当社のスパッタリングにおける特長
当社では、特に自動車業界へのスパッタリングの実績が多数ございます。厳しい品質管理である自動車業界への工程監査もクリアしており、安定した供給が可能です。
メーター関連部品においては、スパッタリング・塗装・レーザーなど、複数の加飾を組み合わせたり、レーザー抜きで光の透過を表現したり、といった様々な対応も可能です。
自動車業界以外にも、スパッタリングの実績も多数存在しますので、お気軽にお問合せ下さい。
スパッタリングの製品事例
メーターパネル(2色成形+メッキ)
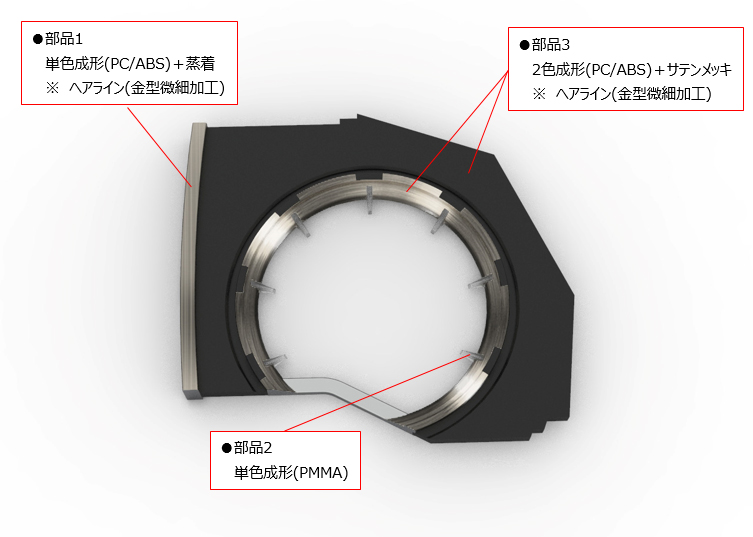
こちらは、車載用メーターパネルにメッキ処理と蒸着を行った加飾事例です。
ABS樹脂とポリカーボネート(PC)の2色成形でパネル部分を成形、そちらに併せてプリズムとオーナメントの3部品をASSYしています。
パネルの目盛部分は金型加工により、微細なヘアライン仕様となっております。
スパッタリングのことなら加飾技術ナビにお任せください!
今回はスパッタリングについてご紹介いたしました。
スパッタリングは、真空状態で処理を行うため、不純物が少ない薄膜成形が可能です。また、緻密で欠陥が少ない高精度な膜を製作でき、加工できる製品に関しても条件が少ないため、様々な製品に膜を付与することが出来る技術です。
加飾技術ナビでは、スパッタリングに関して、試作から量産までワンストップ対応が可能です。また、スパッタリング以外にも、様々な加飾工法の実績がございます。
スパッタリングをはじめ、加飾に関してお困りごとがございましたら、お気軽にご相談ください。
最後までお読みいただき、ありがとうございました!